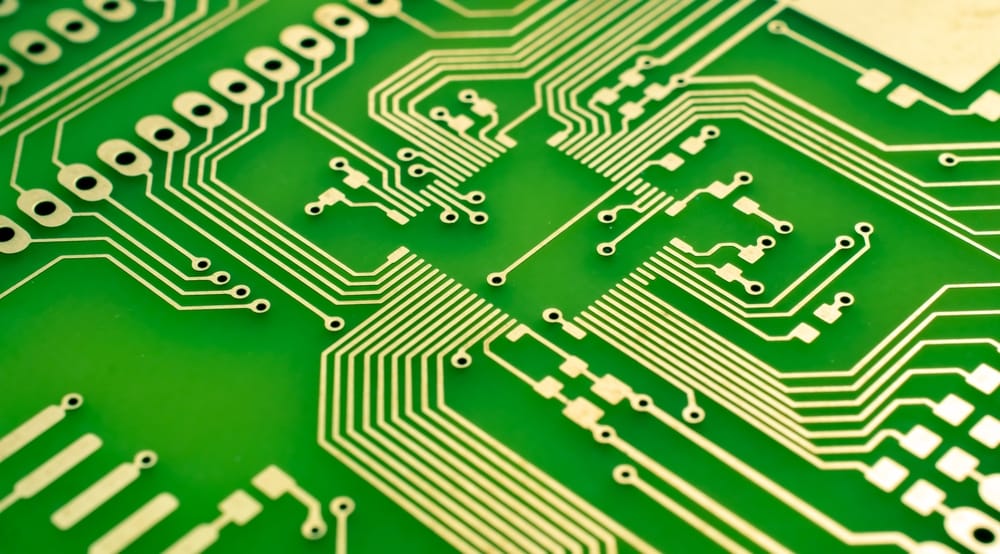
Rigid-Flex PCB Manufacturing: Techniques and Considerations
Rigid-Flex PCBs have gained widespread popularity in the electronics industry due to their ability to combine the benefits of rigid and flexible PCBs into a single, compact, and versatile solution. Manufacturing Rigid-Flex PCBs involves a unique set of techniques and considerations to ensure that the final product meets the stringent quality and reliability standards demanded by various applications. In this article, we will explore the manufacturing techniques and important considerations for Rigid-Flex PCB production. Visit rigid flex rigid PCB to learn more.
Key Manufacturing Techniques for Rigid-Flex PCBs
1. Layer Stackup Design:
The layer stackup of a Rigid-Flex PCB is a critical aspect of the manufacturing process. Designers must carefully plan the arrangement of rigid and flexible layers, considering the number of layers, materials used, and their thickness. The stackup design directly impacts the board's mechanical integrity, electrical performance, and flexibility.
2. Material Selection:
Choosing the right materials is paramount in Rigid-Flex PCB manufacturing. Rigid sections typically use standard FR-4 material, while flexible sections may use polyimide or similar materials known for their flexibility and reliability. Selecting materials with compatible thermal expansion coefficients is essential to prevent delamination and stress-related issues.
3. Etching and Plating:
The process of etching involves selectively removing copper from the PCB substrate to form circuit traces. Etching techniques must be carefully controlled to maintain the integrity of the flexible sections. Plated through-holes and vias are used to establish connections between rigid and flexible layers, requiring precise control to ensure proper conductivity.
4. Coverlay Application:
Coverlay, a flexible insulating material, is applied to protect the flexible sections of the PCB. The coverlay is carefully aligned with the flex-bend areas and must adhere securely without causing wrinkles or bubbles.
5. Mechanical Fasteners and Connectors:
Mechanical fasteners and connectors are employed to secure the rigid sections of the PCB and provide additional support. These components should be chosen based on the specific mechanical and electrical requirements of the design.
6. Laser Processing:
Laser cutting and drilling technology are often used to shape and trim Rigid-Flex PCBs with precision. Laser processing enables clean cuts and precise hole drilling in both rigid and flexible sections.
Important Considerations in Rigid-Flex PCB Manufacturing
1. Flex-Bend Areas:
Designers must carefully identify and mark flex-bend areas, where the PCB will experience bending or flexing during its operational life. Components, traces, and vias should be avoided in these areas to prevent damage.
2. Tolerances and Clearances:
Strict adherence to manufacturing tolerances and clearances is essential to prevent issues like short circuits, interference, and misalignment between rigid and flexible sections.
3. Quality Control:
Quality control measures are crucial at every stage of Rigid-Flex PCB manufacturing. Visual inspections, electrical testing, and flex testing are performed to ensure that the final product meets the required specifications and standards.
4. Thermal Management:
In designs with components that generate heat, adequate thermal management techniques, such as the inclusion of thermal vias, must be employed to prevent overheating and maintain reliability.
5. Environmental Considerations:
Manufacturers should ensure that Rigid-Flex PCBs are built to withstand environmental factors such as temperature extremes, humidity, and vibration, depending on the intended application.
Conclusion
Rigid-Flex PCBs represent a remarkable fusion of traditional rigid PCBs and flexible PCBs, enabling versatile and space-efficient solutions for modern electronics. However, their manufacturing process requires careful planning, precision, and adherence to quality control standards to ensure the reliability and performance demanded by a wide range of applications. By employing the right manufacturing techniques and considering critical design and material choices, manufacturers can produce high-quality Rigid-Flex PCBs that meet the diverse needs of the electronics industry.